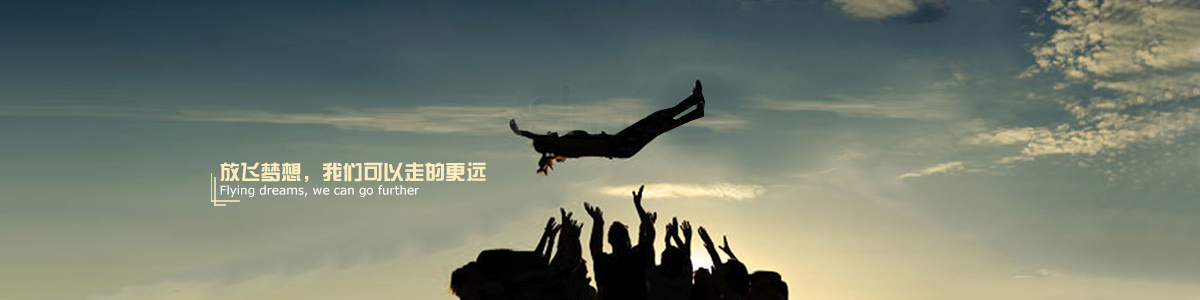

企業新聞
企業新聞
聯系我們
蘭州電機股份有限公司(以下簡稱“蘭電股份”)充分利用“出城入園”契機,圍繞“中國制造2025”,瞄準國際標桿企業先進制造工藝水平,堅持以“綠色化、信息化、智能化”的“三化”改造建設為主攻方向,順應產業發展趨勢和規律,以“基于個性化定制的大中型高效智能化電機數字化車間建設”的國家級項目為抓手,通過基于企業私有云平臺基礎網絡建設支撐的信息化架構,以PLM為研發設計主體,以大中型電機、中小型發電機、特種伺服電機等生產單元為智能制造主體,聚焦信息技術、智能化技術和綠色環保技術嵌入到制造關鍵環節,堅持立足當前與著眼長遠相結合,整體統籌規劃,分步實施、驗證推廣,實現產業全面轉型升級,努力將蘭電股份建設成為國內一流、國際先進的電機及發電機設備研發生產制造基地。
研發方面
(蘭電公司信息化規劃圖)
利用計算機三維工程分析軟件,進行電機設計仿真分析,通過PLM系統的建設以及與ERP企業資源計劃、MES制造執行系統的互聯互通,實現了電機三維設計,機械結構、電磁場及流體分析仿真技術應用,信息采集與優化管理,生產計劃與制造執行的完美結合,使蘭州電機產品進入到全生命周期管理階段,極大的縮短了產品的研發周期,保證研發過程中數據的可追溯性。
加工制造方面
(電機軸柔性生產線)
(全自動立體倉庫)
(全自動數控包帶機)
(全自動雙機聯動沖剪機器人)
(全自動電機端蓋清洗線)
(大型真空侵漆設備)
(數控等離子切割機)
(西班牙FAGOR自動沖剪線)
(德國舒曼數控漲型機)
(精密焊接機器人)
(大型數控臥式車床)
(大型數控臥式車床)
(數控精密切割機)
(成型電火花加工中心)
公司引進的電機軸類柔性生產單元是國內第一條多品種、小批量、柔性化生產的中小型電機智能化軸類加工生產線,實現從取料到粗車、精車、銑鍵槽等加工工序再到檢測的全序智能化生產;電機零部件超聲波清洗單元,實現生產全過程自動化;智能控制VPI真空浸漆系統,實現了浸漆過程中的全數字化、自動控制,有效保證了電機的定轉子絕緣,實現操作過程實時監測,在質量大幅提升的同時,效率提高了30%;通過數控包帶機器人及成型線圈FMS柔性制造系統的引進,實現線圈包帶成型的智能化生產,極大減少了模具數量,使線圈生產效率提高了13%;軸及風扇焊接機器人工作站的引進使焊接質量有了大幅的提升,使焊縫的表觀質量實現了質的飛躍,使鉚焊事業部一次交檢合格率提升了6%。沖剪制造部通過生產線改造及雙機互聯沖壓機器人工作站的引進,實現了從抓料、沖壓、到理片的全自動化生產,提高生產效率23%以上,人員減少40%。
檢測方面
(大中型電機試驗機組)
(大中型電機試驗控制室)
(小型發電機試驗檢測系統控制室)
(瑞典海克斯康三坐標測量儀)
(壓力自動檢測系統)
(熱電偶熱電阻檢定系統)
(漆包線測試儀)
蘭電股份以大中型電機試驗系統建設為試點,中小型發電機、伺服電機試驗站同步推進,融合信息化以DCS試驗站計算監控系統、ATS試驗數據采集分析系統、以及TDS試驗數據管理系統為工具,完成試驗設備的監視、控制、遠程操作,并通過與PLM、ERP、MES的互聯互通實現電機數據的采集、存儲分析、處理,實現電機從設計研發、生產制造、試驗檢測、到維修再制造的全生命周期管理。
蘭電公司通過“出城入園”新園區項目建設及“基于個性化定制的大中型高效智能化電機數字化車間建設”國家項目的實施,新購置和數字化改造各類生產加工設備1200多臺套,主要設備數字化率達到86%以上,先進的工藝設備、檢測儀器覆蓋研發設計、加工制造、過程檢驗、成品試驗等全過程。通過“三化”造改造升級,全公司在崗員工數量減少了30%、生產經營成本降低了15%。隨著研發、制造、檢測設備的升級換代,公司新產品的研發周期由原來的8個月縮短到了5個月;電機生產周期由原來的75天縮短到了50天,總體生產效率提高了約30%;通過能源管理系統的建設投用,實現了能源消耗的定時管理,有效提高了資源利用效率;安全生產管理水平持續提高,搬遷至新園區后無安全事故發故。搬遷兩年來,公司產銷量提高了25%,有11項新產品推向市場。
作為西部電機生產重點骨干企業,蘭電股份將以“三化”改造為主攻方向,持續推進關鍵加工、裝配工序智能化改造升級及“機器替人”的應用,進一步提高工作效率,以市場及技術拓展為引導加強對外合作,不斷提升蘭電股份產品的研發及制造能力,進而提升企業綜合競爭力,為甘肅裝備制造業高質量發展做出更大的貢獻。
掃二維碼用手機看